Versatile bonding for lightweight components
New materials are making cars, planes and all sorts of other things lighter. The catch is that many of these materials can’t be welded. Now there’s an alternative joining me- thod available – gradient adhesives provide an extremely good way of ensuring joined parts stay joined for their entire service life and hold up well in the event of a crash.
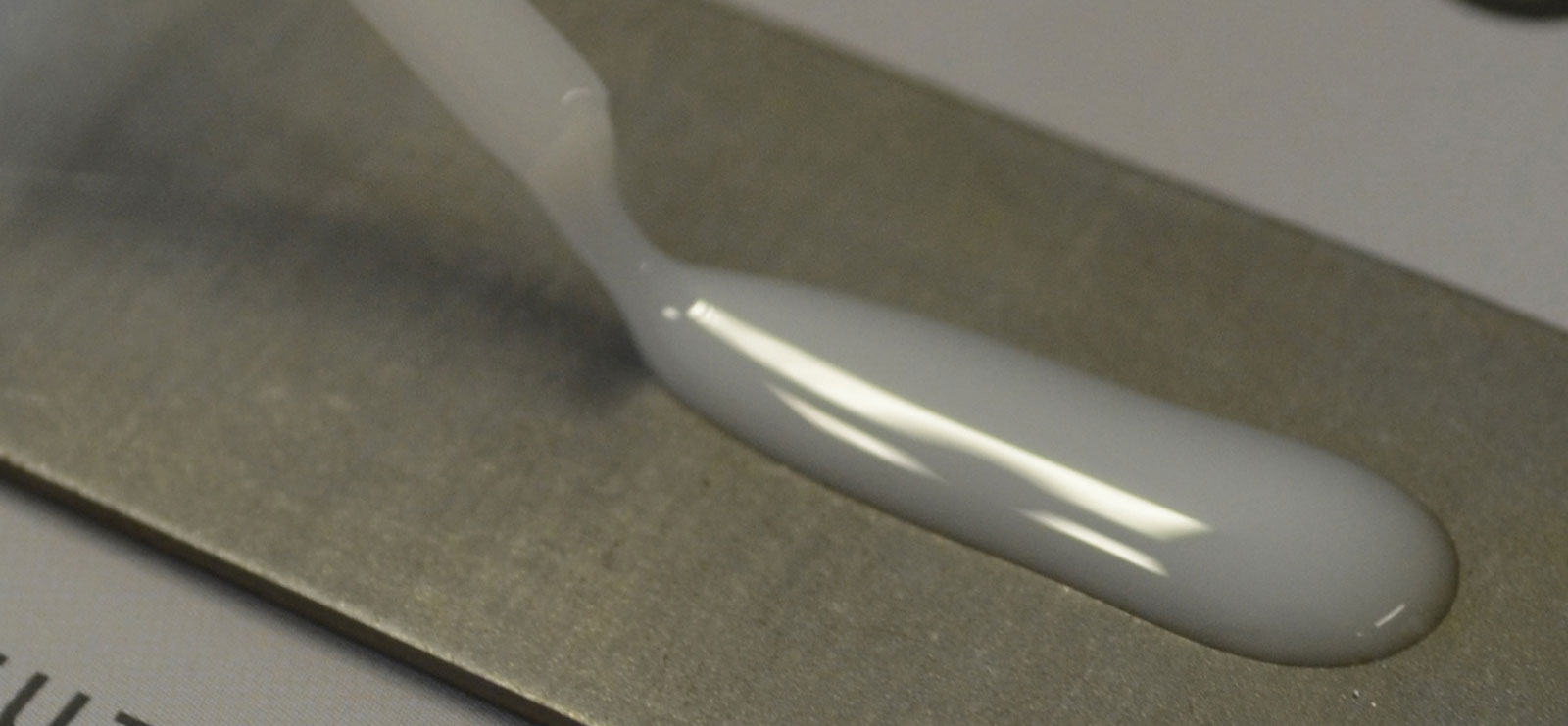
Shedding pounds is all the rage these days and the global trend toward weight reduction has even spread to the automobile industry. Cars are to get even lighter – using new materials such as ultra-high-strength steels or carbon, and carbon-fiber-reinforced plastics (CFRP). But no matter which diet regime and which lightweight components manufacturers choose, they all want the same thing: the best and longest-lasting joining method for vehicle components. Since Duroplast, which often serves as the matrix component for CFRPs, can’t be welded, another joining technique is called for.
Bonding is the best solution. “We work primarily with structural adhesives, which bond components permanently and create additional shape stability,” says Dr.-Ing. Jan Spengler, a chemical analyst in the Plastics division at the Fraunhofer Institute for Structural Durability and Reliability LBF in Darmstadt. These adhesive bonds offer a particular advantage; they hold up considerably better in crashes than other types of bonds. What’s more, adhesives possess better damping characteristics than metal and improve noise vibration harshness (NVH). NVH is the term for what car occupants perceive as vibration or hear as noise. “The adhesive layer functions like a classic damper, which saves on insulation material and reduces weight,” says Dr.-Ing. Halvar Schmidt from the LBF’s Structural Durability division.
Rigid and elastic at the same time
Both the Plastics and Structural Durability divisions at the LBF have been researching dual cure adhesives for the past year and a half. What makes them special is that they harden in two phases. For gradient adhesives like these, humidity, heat, anaerobic conditions or UV light trigger the first stage of the hardening process. Another activator can be used to initiate a secondary hardening process. “This kind of adhesive has been available on the market for some time, but up to now the products have always provided a constant elasticity and the same rigidity at every point,” reports Spengler. “We’ve succeeded in manufacturing an innovative dual-cure adhesive with variable elasticity.” The first heat-triggered hardening mechanism coats the entire adhesive surface, resulting in a soft, flexible product. A second hardening process begins when it is exposed to UV light. What makes it special is that this reaction can be contained to very specific areas. The adhesive’s polymer chains crosslink where it is exposed to UV light, creating a localized area with greater rigidity. In this way, the LBF researchers have produced a bonded plastic with one very soft and one very hard half.
Thanks to the gradient rigidity, the innovative adhesive can achieve a significantly prolonged bond. This is important, considering that every trip a vehicle makes subjects the car to vibration loads, and such external stress is always distributed unevenly across the bond. What then happens is that joints develop stress peaks at the edges, and the bond is highly stressed. “Our newly developed adhesive with gradient rigidity is elastic on the outer edges and handles stresses better and stress peaks are absorbed,” explains Spengler. “But in the middle, the adhesive layer has been spot-cured and is correspondingly rigid, which ensures that the bond and the adhered vehicle chassis maintain continuous shape stability.