Automatica 2014
Flugzeugtragflächen automatisiert montieren
Flugzeugtragflächen werden bislang manuell montiert. Künftig lässt sich der Prozess automatisieren. Ein neuartiger, schlangenförmiger Roboter gelangt selbst in die hintersten Winkel der Tragflächen, um dort Komponenten zu verschrauben.
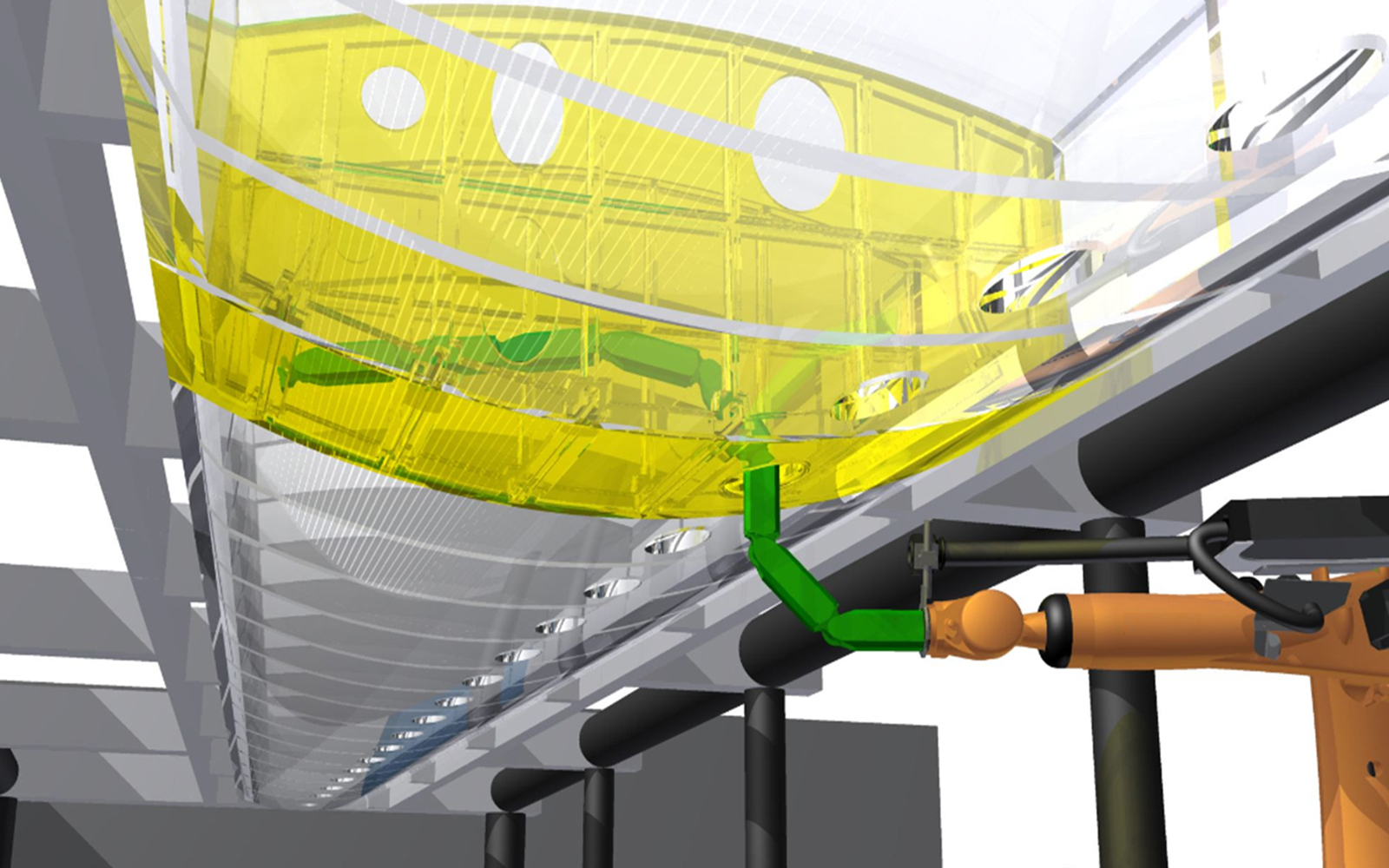
Das Flugaufkommen hat in den letzten Jahrzehnten rasant zugenommen. Der Flugzeughersteller Airbus geht davon aus, dass es sich bis 2030 verdreifachen wird. An einem einzigen Tag verzeichnet beispielsweise der Frankfurter Flughafen mehr als 1300 Starts und Landungen. Dies entspricht einer Passagieranzahl von ungefähr 155 000 pro Tag alleine in Frankfurt. Um den entsprechend hohen Bedarf an Transportmitteln zu decken, ist eine Modernisierung der Fertigungsabläufe im Flugzeugbau unumgänglich.
Bislang erfolgt die Flugzeugmontage überwiegend noch per Hand. Um die Produktion anzukurbeln, müssen manuelle Abläufe automatisiert werden. Bei einigen Prozessen im Flugzeugbau ist das problemlos möglich, bei der Montage der Tragflächen hingegen sind die Flugzeugbauer herausgefordert. Der Grund: Diese erfolgt vor allem im Innern der Tragflächen – in nebeneinander angeordneten Kammern. Zugang zu diesen Arbeitsräumen gewähren Mannlöcher – für das Montagepersonal ist es sehr mühsam, durch die nur 45 Zentimeter langen und 25 Zentimeter breiten Öffnungen in die Tragflächen zu klettern, um dort die Tragflächenkomponenten mit Passschrauben zu befestigen und Nahtstellen abzudichten. Pro Tragfläche fallen rund 3000 Passbohrungen an. Dementsprechend zeitaufwändig, körperlich anstrengend und ermüdend ist die Prozedur. Hinzu kommen gesundheitliche Belastungen durch Dämpfe, die beim Abdichten entstehen.
Schlankes, verschränkungsfähiges Robotersystem für Innenräume
Konventionelle Industrieroboter gelangen nicht durch die engen Öffnungen. Mit ihren starren Gliedern erreichen sie auch nicht den hintersten Winkel der bis zu fünf Meter langen Arbeitsräume. Erforderlich ist ein schlanker Roboter, der zudem verschränkungsfähig ist. Ein solches Modell mit beweglichen Gliedern entwickeln Forscher am Fraunhofer-Institut für Werkzeugmaschinen und Umformtechnik IWU in Chemnitz. »Der Roboter besteht aus acht Achsgelenken. Durch die seriell verketteten kurzen Dreh- und Kippgelenke kann er sehr enge Bahnradien abfahren und sich in die entlegensten Ecken der Kammern schlängeln. Wir nennen ihn auch Schlangenroboter«, sagt Marco Breitfeld, zuständiger Projektleiter am IWU.
Am vordersten der acht Glieder wird das Werkzeug befestigt – alternativ lässt sich auch eine Kamera für Inspektionsaufgaben anbringen. Der insgesamt zweieinhalb Meter lange Roboter ist in der Lage, bis zu 15 Kilogramm schwere Werkzeuge zu tragen – zusätzlich zu seiner Eigenlast.
Angetrieben wird die Roboterkinematik durch einen ausgetüftelten Mechanismus – das Getriebe wird derzeit zum Patent angemeldet: Aufgrund der kompakten Bauweise der einzelnen Roboterglieder scheidet ein konventioneller Motor aus. Breitfeld und sein Team haben in jedem der acht Glieder einen sehr kleinen Motor verbaut – dennoch bringt es der Antrieb auf ein sehr hohes Drehmoment von bis zu 500 Newtonmeter. In Kombination mit Seilzug und Spindeltrieb ermöglicht er die hohe Beweglichkeit der einzelnen Glieder, die sich jeweils in einem Bereich von 90 Grad verdrehen lassen. »Das Antriebskonzept erlaubt einen Einsatz überall dort, wo hohe Kräfte und Momente auf engstem Raum benötigt werden. Im Flugzeugbau, aber auch im automobilen Karosserie- oder im Kraftwerksbau braucht man solche kompakten Automatisierungslösungen«, so Breitfeld.
Geplant ist, den 60 Kilogramm schweren Roboter auf eine mobile Plattform oder eine Schiene zu montieren, so dass er unter den Tragflächen entlangfahren und sich in jede der Kammern schlängeln kann. Hierfür kann man beispielsweise auf mobile Roboterplattformen zurückgreifen, wie sie im EU-Projekt VALERI kürzlich vom Fraunhofer-Institut für Fabrikbetrieb und Automatisierung IFF vorgestellt wurden. Derzeit testen die Forscher vom IWU das mechanische Konzept sowie die Steuerung. Vom 3. bis 6. Juni präsentieren sie auf der Messe Automatica in München einen Demonstrator des Innenraumroboters (Halle B4, Stand 228). Bis Ende 2014 soll ein Komplettaufbau des mit acht Robotergliedern ausgestatteten Systems entstehen.