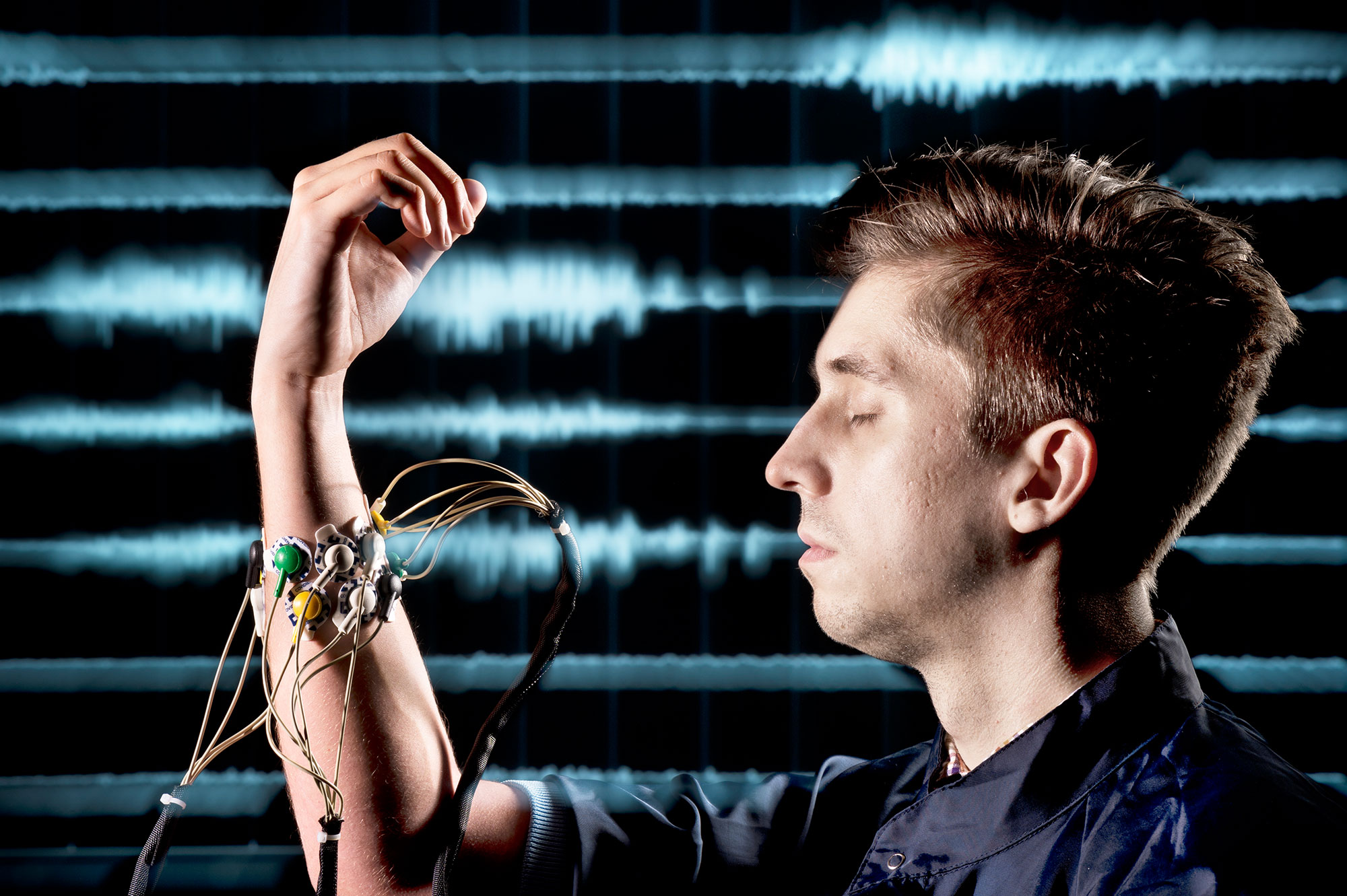
Complex and invasive, theranostatic implants present one of the greatest medical engineering challenges. They must be tested thoroughly at an early turn during the inceptive development phase in the lab. This is a job for Dmitry Amelin, a biomedical engineer at Fraunhofer IBMT. He attaches eight electrodes to his left forearm in preparation for the tests. The electrodes connect to a small box on his desk. Amelin pinches his thumb and index finger together like a pair of tweezers and watches the monitor for the signals that the electrodes are picking up from his muscles. “We are working on the control system for a hand prosthesis. The small box containing all the control circuitry will later be implanted in the patient’s forearm stump,” explains Amelin.
This little box contains a lot more than that – the experience Fraunhofer IBMT gained over decades devoted to building intelligent implants. This know-how encompasses wireless signal and power transmission, mounting and interconnecting technology, and biocompatible encapsulation. As it turns out, developing and producing the electrodes for implants to communicate with the human nervous system is something of an art.
In the lab, the electrodes serving to control the hand prosthesis cleave to the skin’s surface over the muscles. They will later be implanted subcutaneously, directly under the amputee’s fascia. The software counterpart to the implant’s electronic hardware detects the movement pattern and sends the appropriate control signals to the prosthesis, which then also pinches the thumb and index finger together.
This is one direction of communication between human and prosthesis. “What’s groundbreaking about our design is that the prosthesis also gives the wearer sensory feedback,” explains Prof. Klaus-Peter Hoffmann, head of the Biomedical Technology Department at Fraunhofer IBMT. To this end, the scientists installed sensors in the prosthesis that are then connected to the human nervous system. “We developed double-sided filament electrodes that are as fine as hair and attach directly to the nerve,” adds Hoffmann. This should enable the patient to feel the amount of pressure the prosthesis is exerting; that is, the firmness of its grip. And it should be able to do this in real time. It will surely be another ten to fifteen years before this technology makes it out of the lab. But the first preclinical trials are already underway.
Hoffmann’s team has been looking into the art of controlling hand prostheses in a host of projects that go all the way back to 2002. Fraunhofer IBMT and twelve other Fraunhofer Institutes have joined forces in a lighthouse project called Theranostic Implants, which has been making remarkable progress. One research group within this lighthouse project succeeded in developing an intelligent hip prosthesis. Its on-board sensors and actuators enable the doctor to monitor the prosthesis’s fit and readjust it when necessary. A third subproject produced a sensor implant to continuously monitor blood pressure.
The electrodes on the implant that Dmitry Amelin is testing are still connected by way of wires. The next challenge is to develop micro-implants that merge the electrode and implant into one device, thereby eliminating cables and connectors. Of course, synchronized activities require wireless communication between the micro-implants. However, Hoffmann is unwilling to use the usual radio signals to this end for one terrifying reason: “Pacemakers have already been hacked in the USA. Instructions for hacking cochlear implants for the hearing impaired are also circulating on the Internet.” This prompted Fraunhofer IBMT to start investigating ultrasound communication for intelligent implants in the newly launched I-call project.
Secure transmission and storage of sensitive data is becoming increasingly important. This is why Fraunhofer has joined forced with partners in the healthcare sector (see page 15) to develop the Medical Data Space. An IT platform that dovetails diverse medical data would be a boon to diagnosis and therapy.
Twelve Fraunhofer Institutes led by the Fraunhofer Institute for Biomedical Engineering IBMT have joined forces to work on the Fraunhofer lead project “Theranostic Implants”. Until now most implants have been of the purely passive type – a typical example is orthopedic devices for bone repair. But there is a growing interest in active “theranostic” implants that combine therapeutic and diagnostic functions in a single medical device. These devices create a closed feedback loop in which vital parameters are recorded and provide the input for therapeutic intervention.