Has the fuel cell drive achieved technological maturity?
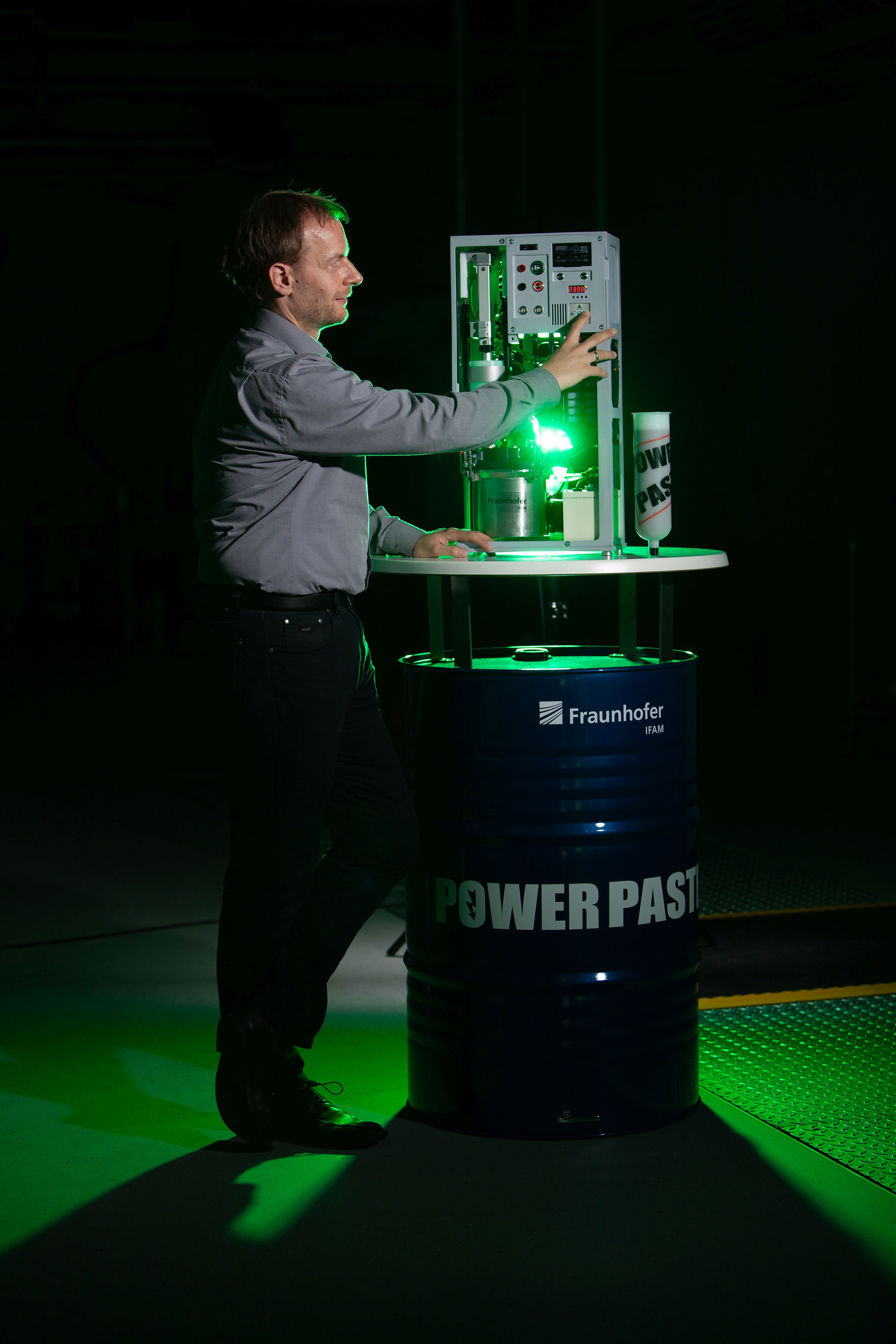
Among hydrogen-powered drive systems, the fuel cell is the most familiar. All of the H2-powered cars currently on the market are equipped with this type of drive: the Toyota Mirai, Hyundai NEXO, Hyundai ix35 FCEV and Mercedes-Benz GLC. Technologically speaking, the fuel cell reverses the process of electrolysis: hydrogen reacts with oxygen to form water, thereby producing electrical energy, which is then used to drive an electric motor. As in the case of electrolyzers, fuel cells are still largely manufactured by hand. However, if fuel cells are to become a standard feature of automotive engineering, an inexpensive method of production is required.
Each car requires much more than just a single fuel cell. A 100-kilowatt vehicle, for example, is equipped with a stack of 400 fuel cells. Given that each day, anything between 1000 and 1500 cars roll off the assembly line in a single automobile plant, it is evident that the scale of fuel cell production must enter a whole new dimension. In terms of cost, too, mass production is vital, as it is only in excess of around 100,000 stacks a year that production for a high-volume use in automobile manufacture will become cost-effective. For this, however, a large number of unresolved production issues must still be determined. This is one of the tasks currently facing the Fraunhofer Institute for Production Technology IPT. “We are creating a research infrastructure that will enable us to run through the entire production process on an industrial level,” says Dr. Christoph Baum, managing chief engineer of Fraunhofer IPT. This will replicate the production process in such a way as to eliminate upscaling risks at each of the individual stages of production.”
The EU project Fit-4-AMandA – “Fit for Automatic Manufacturing and Assembly” – illustrates the extent to which – and, above all, the speed at which – it is possible to enhance the production of fuel cell stacks. It took just two years for an international project team, including Fraunhofer IWU, to develop an automated assembly line for PEM stacks on behalf of the company Proton Motor Fuel Cell. “This boosts production capacity from currently 300 to as many as 5000 stacks a year, depending on stack size,” explains Sebastian Porstmann from Fraunhofer IWU. “At the same time, it reduces assembly times by as much as 95 percent and assembly costs by as much as 90 percent.” Indeed, with slight adjustments to machinery layout, it may be possible to increase production volumes to as high as 30,000 stacks a year. The automated assembly line was jointly developed by the six project partners and delivered to Proton Motor Fuel Cell at the end of May 2019. The Fraunhofer research team was responsible for a number of aspects, including a profitability study, an analysis of the manufacturing process for bipolar plates and a risk assessment to determine the risks involved in supplying bipolar plates to a market that is only just emerging.
In HOKOME, another Fraunhofer project, five institutes – IWU, ISE, IWS, IKTS and IPT – are seeking to upscale production to an industrial level with technologies that enable the manufacture of between 50 and 60 stacks per minute. “What’s more, our production method can bring cost savings of up to 50 percent,” says Scheffler from Fraunhofer IWU. “We’re now using a roll-to-roll process to coat the MEA – the membrane electrode assembly – which is one of the two main components of the fuel cell.” The second of these components, the bipolar plate, is manufactured from a sheet of stainless steel only 0.05 to 0.1 millimeters in thickness – about as thin as kitchen tinfoil. As the sheet unwinds from a roll, the anode and cathode are produced in parallel by means of a forming process and then directly joined together to form the bipolar plate. In spring 2021, this method will transfer from the laboratory to an environment with conditions close to those of mass production.
When it comes to solid oxide fuel cells, there are various cost drivers. These include manual fabrication and the use of parts made of expensive materials, such as ceramic components in the supply lines. However, researchers at the Fraunhofer Institute for Mechanics of Materials IWM have now discovered a way of coating steel that increases its resistance to hydrogen, compared to noncoated steel, by a factor of around 3500.