Ist die Brennstoffzelle als Autoantrieb ausgereift?
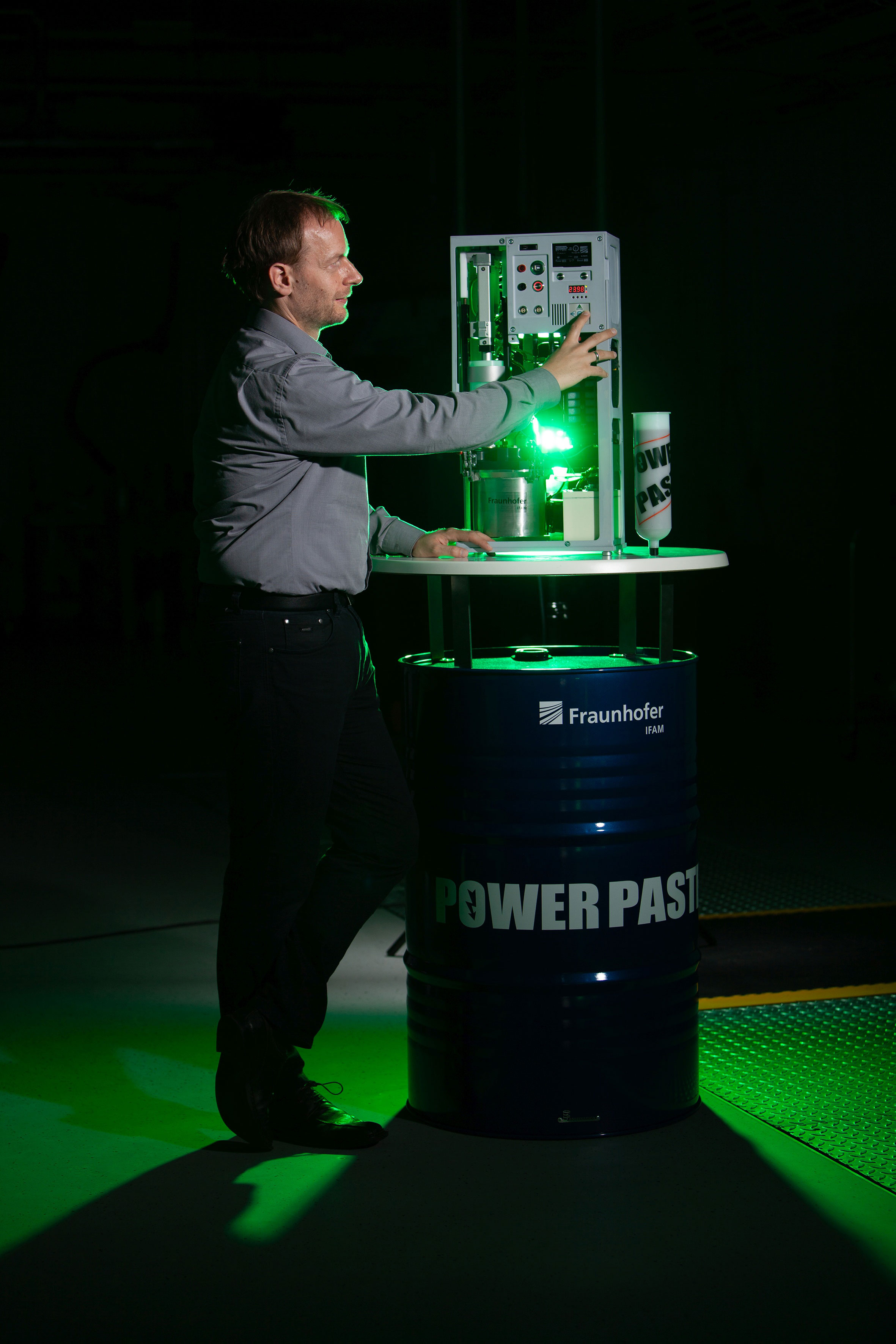
Spricht man von Wasserstoff-Antrieben, ist der bisher bekannteste die Brennstoffzelle. Schließlich basieren alle H2-betriebenen Autos, die derzeit auf dem Markt sind, darauf: der Toyota Mirai und der Hyundai NEXO ebenso wie der Hyundai ix35 FCEV und der Mercedes-Benz GLC. Technologisch ist die Brennstoffzelle die Umkehrung der Elektrolyse: Der Wasserstoff reagiert mit Sauerstoff zu Wasser, dabei entsteht elektrischer Strom, der in einem Elektromotor umgesetzt wird. Ebenso wie die Elektrolyseure werden auch die Brennstoffzellen noch weitestgehend im Manufakturbetrieb hergestellt. Doch: Sollen Brennstoffzellen standardmäßig in Autos verbaut werden, ist eine kostengünstige Produktion nötig.
Schließlich wird bei Weitem nicht nur eine Brennstoffzelle pro Auto benötigt – vielmehr stapelt man bei einem 100 Kilowatt-Auto 400 Brennstoffzellen übereinander zu einem Stack. Dass in einem Autowerk pro Tag rund 1000 bis 1500 Autos vom Band laufen, macht überdeutlich, in welche Bereiche die Serienfertigung der Brennstoffzellen vordringen muss. Auch was die Kosten angeht, ist Massenherstellung nötig: Erst ab ca. 100 000 Stacks pro Jahr wird die Produktion für den breiten Einsatz in Pkw wirtschaftlich. Dafür sind viele unbewältigte Produktionsaufgaben zu lösen. Dieser Herausforderung widmet sich unter anderem das Fraunhofer-Institut für Produktionstechnologie IPT. »Wir bauen eine Forschungsinfrastruktur auf, auf der wir die komplette Fertigung auf einem industriellen Level durchspielen können«, sagt Dr. Christoph Baum, Geschäftsführer am Fraunhofer IPT. »Die Produktion wird dort so nachgebildet, dass für jeden einzelnen Prozessschritt keinerlei Skalierungsrisiken bestehen.«
In welchem Maße – und vor allem wie schnell – sich die Fertigung von Brennstoffzellen-Stacks optimieren lässt, zeigt auch das EU-Projekt Fit-4-AMandA, kurz für »Fit for Automatic Manufacturing and Assembly«. In nur zwei Jahren gelang es dem internationalen Projektteam – mit dabei auch das Fraunhofer-Institut für Werkzeugmaschinen und Umformtechnik IWU –, eine Anlage zur automatisierten PEM-Stack-Montagelinie für die Firma Proton Motor Fuel Cell GmbH zu entwickeln. »Diese erhöht die Fertigungskapazität je nach Stack-Größe von 300 auf aktuell bis zu 5000 Stacks pro Jahr«, sagt Sebastian Porstmann vom Fraunhofer IWU. »Gleichzeitig können damit die Montagezeit um bis zu 95 Prozent und die Montagekosten um bis zu 90 Prozent verringert werden.« Mit leicht geändertem Maschinenlayout könnten perspektivisch sogar bis zu 30 000 Stacks jährlich hergestellt werden. Die Anlage, die dies ermöglicht, wurde Ende Mai 2019 an die Proton Motor Fuel Cell GmbH ausgeliefert – entwickelt wurde sie gemeinsam von den sechs Projektpartnern. Das Fraunhofer-Forscherteam widmete sich unter anderem der Wirtschaftlichkeitsbetrachtung, der Analyse von Fertigungsverfahren für Bipolarplatten und der Risikoanalyse: Wie sicher ist die Zulieferung der benötigten Bipolarplatten in einem Markt, der gerade erst entsteht?
Auch im Projekt HOKOME wollen fünf Fraunhofer-Institute – IWU, ISE, IWS, IKTS und IPT – weg vom bisherigen Manufakturbetrieb in industrielle Bereiche vorstoßen: Mit Technologien, die eine Produktion von 50 bis 60 Stacks pro Minute erlauben. »Zudem sind mit unserer Herstellungstechnik Kosteneinsparungen von bis zu 50 Prozent möglich«, weiß Sören Scheffler vom Fraunhofer IWU. »Wir setzen beim Beschichtungsprozess der Membran-Elektrodeneinheit MEA – einer der beiden Hauptkomponenten der Brennstoffzelle – komplett auf das Rolle-zu-Rolle-Verfahren«, erläutert der Fraunhofer-Experte. Die zweite Hauptkomponente, die Bipolarplatte, wird aus einer etwa 0,05 bis 0,1 Millimeter dünnen Edelstahlfolie gefertigt, ähnlich dünn wie die aus der Küche bekannte Alufolie. Abgewickelt von einer Rolle folgt der parallele Umformprozess für Anode und Kathode, die sofort anschließend zur finalen Bipolarplatte zusammengefügt werden. Im Frühjahr 2021 soll die Technologie vom Labor in die seriennahe Einsatzumgebung überführt werden.
Weiterer Kostentreiber neben der Manufakturfertigung sind bei Festkörperoxid-Brennstoffzellen Komponenten aus teuren Materialien, etwa keramische Bauteile in den Zuleitungen. Forscher am Fraunhofer-Institut für Werkstoffmechanik IWM haben nun eine Möglichkeit gefunden, den Stahl so zu beschichten, dass er den Wasserstoff rund 3500-mal stärker zurückhält als unbeschichteter Stahl.