High-speed 3d printer for high-performance plastics
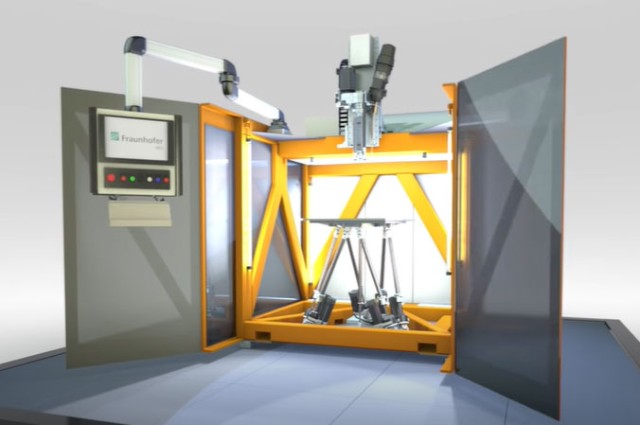
In the last few years, a 3D printing process has been developed at the Fraunhofer Institute for Machine Tools and Forming Technology IWU that resolves a significant disadvantage of the technology: It is considerably faster than conventional processes, which means it can enable flexible production in times of crisis. Researchers at Fraunhofer IWU had the idea to combine a plastic injection unit with 3D printing, which speeds up the process considerably. The system was equipped with a movable table that quickly moves back and forth beneath the nozzle, which ensures that the liquid plastic is assembled into a 3D component at high speed. This concept, called SEAM, has already been used by a number of manufacturers. “With this method, we can produce a strand of material about one meter long every second,” says developer Christopher Schlegel. All in all, it reduces production time by up to 70 percent compared to conventional systems. SEAM technology is especially suited to large, plastic components up to ten meters long. Large structures for vehicles and trains, for example, can be produced quickly and cheaply using this method. The same applies to tools and clamping mechanisms for the production of plastic components. Fraunhofer IWU is cooperating with numerous industry partners involved in automobile and machine construction. The system is so small that it can be packed into a container and brought to the application site in case of an emergency. Once on site, it will be able to produce plastic parts as required.
Markus Heilemann from the Fraunhofer Research Institution for Additive Manufacturing Technologies IAPT is working on these 3D printing containers together with his team. “The system is tailored directly to the container. In essence, the container itself is the 3D printer,” he explains. Fraunhofer IAPT experts are deploying a variety of printing technologies, including plastic printing, printing with metal powder and printing with metal wires. Systems that produce materials by welding together different horizontal layers are of particular interest, as they can be used to repair components in emergencies. The goal of the developers was to design containers that, once fully manufactured and calibrated, would work as simply as pushing a button. “In the future, such containers could produce replacement parts for engines or turbines in factories, oil rigs and poorly developed regions,” says Heilemann. This could help avoid production losses, which often run up to millions of euros. The technology has also proved its capabilities. Last year, there was a crisis when the supply of respiratory masks fell short. The team at Fraunhofer IAPT abruptly switched to producing plastic adapter units. “These enabled us to connect simple diving masks used by hobby snorkelers up to ventilators,” says Heilemann. The container used for the production of medical technology components has been named “MobiMed.”