Palm trees, pristine beaches, a crystal clear ocean: Christoph Pöhler is enjoying his vacation on the Fiji islands thousands of miles away. Yet civilization soon catches up with the engineer on his stand-up paddle board (SUP): His suddenly finds himself paddling between flip flops, washing-detergent bottles and parts of a surfboard. Yet this piece of sports equipment, on which he was hoping to relax, is also made of plastic, hardly likely to be recycled in this far flung corner of the world. Pöhler doesn't want to be part of the problem for very much longer: And so the idea for the ecoSUP was born. His vision: a SUP consisting of nothing but renewable raw materials. The PhD student found the perfect setting for his idea at the Fraunhofer Institute for Wood Research, Wilhelm-Klauditz-Institut WKI. Fraunhofer WKI has a unique method for producing wood foams. The researchers there also experiment with components made from natural fibers and specialize in process engineering, natural-fiber composite plastics and surface technologies for wood preservation and emission control. And of course, recycling processes are another area of research at the Fraunhofer Institute in Braunschweig. Having received initial funding for the exploratory phase from the Federal Ministry of Education and Research (BMBF), Pöhler now plans to move his project to the next level through a crowdfunding campaign on the Startnext platform. We talked to the impassioned scientist, water sports enthusiast and savior of the world about the particular challenges he faces and what's next on the agenda for ecoSUP.
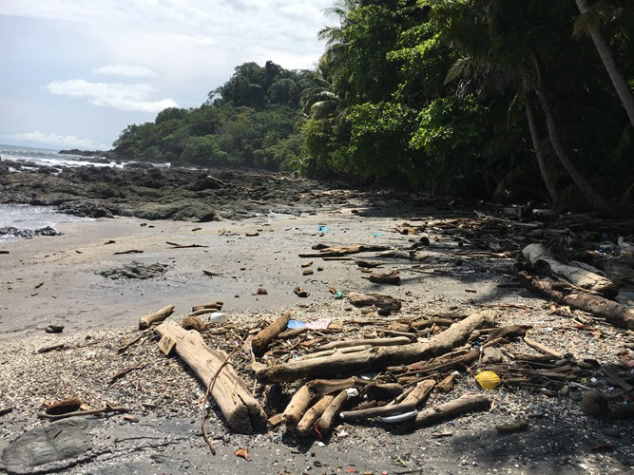
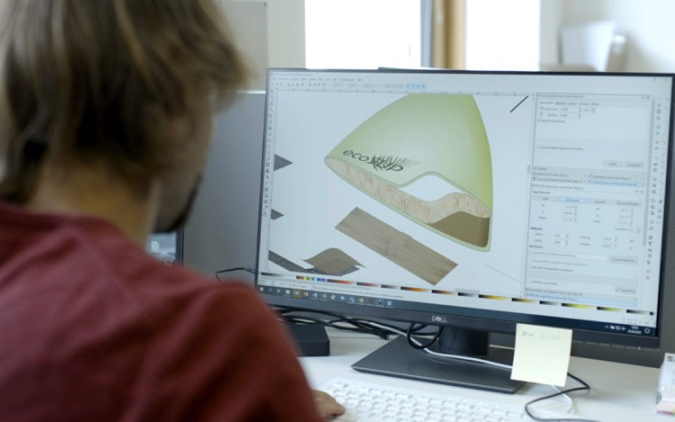
Please, Tell us more about your idea of a 100 percent bio-based stand-up paddle board?
Its structure is similar to that of a conventional surfboard. Normally, a polystyrene core, which we know as styrofoam, is reinforced with fiberglass and sealed with an epoxy resin. The approach is cost-effective and manufacturing processes are optimized for these materials. The product properties deliver high rigidity and stability. The ecoSUP project, though, is about developing plant-based alternatives to these materials, which are not exactly environmentally friendly.
One of our objectives, beyond that, is to simplify the process so that any existing production equipment can still be used with our renewable materials. If the level of investment is too high to start with, it will be difficult to get the idea of this process across. Of course, it's always tempting to develop a product that could turn out to be a hit. But we should never lose sight of the economic viability. That's why we are concentrating on developing materials and methods that can be used in established processes.
Is there a problem building a paddle board from wood?
There are a number of criteria. The board has to be transportable, we have to balance rigidity and weight. Wood gives us plenty of rigidity, but at the expense of weight. Our indigenous types of wood have a high density (Mostly spruce or beech in Germany). So to achieve the necessary buoyancy, the board would be extremely large and this would make it too heavy. You could make the floating body hollow and use wood just on the outside, but you would soon be at the limit of economic viability. This kind of construction is highly labor intensive, and in my view, large scale production would be barely viable. In other words, the end product would simply be too expensive for most customers.
What are the main obstacles?
We definitely consider the development of the biopolymer to be one of the biggest challenges. We are of course trying to unite various objectives or product properties. The bio-based material we are looking for has to be durable in a number of respects. It will be exposed to UV radiation, a range of different temperatures and saltwater - always a critical aspect for polymers. If we use natural fibers, we are also limited in terms of process temperatures. That's why our focus is on thermosetting polymers, as these compounds do not have to be melted for reshaping. AND, ideally, the material is readily recyclable or biologically degradable at the end of its life cycle. So we have very little choice when it comes to the resin. Working with chemists from Fraunhofer WKI, we are looking to develop a proprietary 100 percent bio-based and durable biopolymer with itaconic acid. This acid consists of tiny molecules and can be obtained relatively cheaply and in large quantities from agricultural by-products.