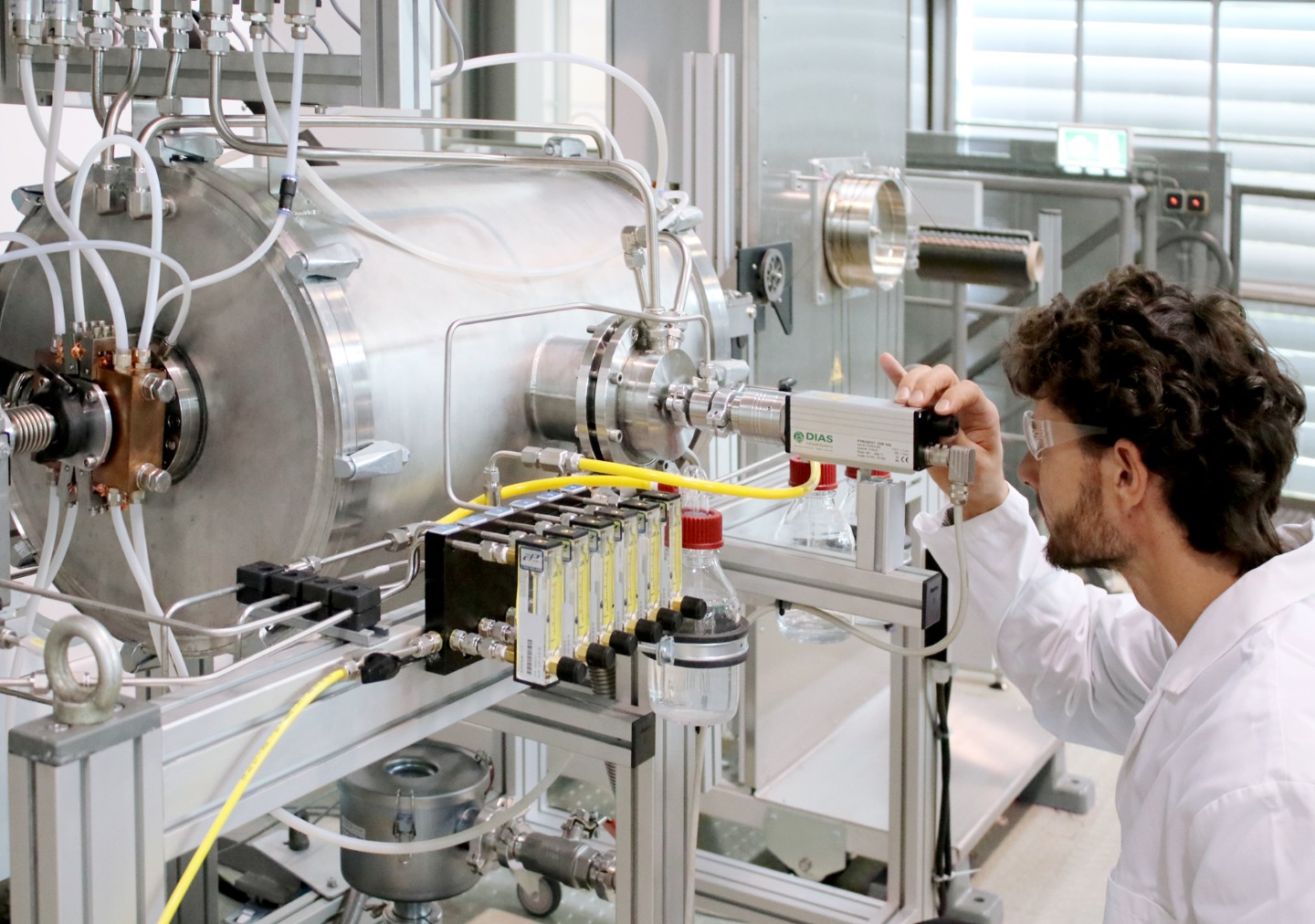
Carbonfasern werden aus polymeren faserförmigen Vorläufermaterialien hergestellt, den Präkursoren. Gegenwärtig basieren 95 Prozent der Carbonfasern auf dem Weltmarkt auf erdölbasiertem Polyacrylnitril (PAN) als Präkursor. Neuartige biobasierte Carbonfasern können ihnen inzwischen fast das Wasser reichen.
Carbonfasern, auch Kohlenstofffasern oder C-Fasern genannt, sind das festeste und steifste Material, das derzeit in großtechnischen Anlagen erzeugt werden kann. Dies sowie ihr geringes Gewicht machen sie heute vor allem im Leichtbau zur Verstärkung von Kunststoffen unersetzlich. Hier vollbringen sie in stark beanspruchten Bauteilen wahre Höchstleistungen – beispielsweise in Flugzeugen, Autos, Sportgeräten oder Windkraftanlagen. Mit Blick auf globale Umweltaspekte wächst im Bereich des Leichtbaus allerdings die Nachfrage nach biobasierten und nachhaltigen Hochleistungsmaterialien. Zwar gibt es bereits erste biobasierte Carbonfasern, allerdings haben sie gravierende Nachteile. Erstens die schlechte Materialausbeute: Bisher werden nur etwa 10 bis 30 Gewichtsprozent des Präkursors zur Carbonfaser, je nach eingesetztem biobasiertem Rohstoff. Zweitens der geringe Anteil an geordneten Kohlenstoffstrukturen in der Carbonfaser. Und drittens die geringe Orientierung der geordneten Kohlenstoffstrukturen entlang der Faserachse – sie bestimmt maßgeblich die Eigenschaften der Faser.
»Wir haben uns aller drei Nachteile angenommen und forschen unter anderem mit Partnern aus der Industrie erfolgreich an praktischen und ökonomischen Lösungen«, sagt Dr. Jens Erdmann, Faserspezialist am Fraunhofer-Institut für Angewandte Polymerforschung IAP. »Die größte Herausforderung liegt darin, die mechanischen Eigenschaften, insbesondere Festigkeit und Steifigkeit, der biobasierten Carbonfasern um ein Vielfaches zu steigern«, sagt Erdmann. Dafür haben Erdmann und sein Team einen speziellen Ultrahochtemperaturofen anfertigen lassen, in dem die biobasierten Carbonfasern zusätzlich für wenige Sekunden bei Temperaturen zwischen 2700 und 2900 °C thermisch nachbehandelt werden. »In diesem Temperaturbereich lassen sich die Kohlenstoffstrukturen in der Faser durch Verstrecken so anordnen, dass sie in Richtung der Faserachse orientiert sind. Das macht die Fasern deutlich fester und steifer und sie erhalten mechanische Eigenschaften, die das Niveau erdölbasierter Carbonfasern erreichen. Wir erhalten sogenannte High-Modulus-Fasern«, erklärt Erdmann. Mit dem neuen Ofen eröffnen sich viele neue Möglichkeiten, um leichte und stabile Materialien zu entwickeln.